Overview
True to its unconventional designation, shale development requires new ways of working: new operations, new well designs, and even new science. While we haven’t discovered any new physics, the geomechanics of unconventional reservoirs has been largely overlooked in the realms of geoscience.
As a data scientist, I’ve been part of analyzing well spacing for several years – combining a multitude of factors across disciplines. It wasn’t until I started working with Dr. Mark Zoback that I realized we were approaching the problem without the most important ingredient: Geomechanical Stress.
In this post, I’ll explain how vertical geomechanical stress profiles can be extracted from ISIP measurements and used throughout an asset to optimize well spacing. This is a perfect activity for engineers and geoscientists while the rig count is down and the organization has time to update its plan. At Petro.ai, we have built a new tool that facilitates fast and accurate ISIP measurement.
Advances in Geomechanics
Dr. Zoback spent his early career measuring and characterizing the state of stress in the earth, which he applied successfully to wellbore stability problems all around the globe. Prior to tight reservoirs, breaking rock largely fell in the lap of drillers, with very minimal productive hydraulic fracturing. Interestingly, Dr. Zoback’s research was used to prevent a well from hydrofrac’ing while drilling.
Because of Dr. Zoback’s pioneering work in measuring and applying the state of stress, our industry has been able to drill more complex, deeper wells through a variety of formations and stress regimes. These techniques are now canon in the drilling doctrine. However, in the development of a shale asset, in which we fracture the entire length of the contact within the pay zone, we did not apply the same principles. As a result, we’ve assumed that when it came to frac’ing, bigger was better.
The Problem of Well Spacing
As it turns out, bigger isn’t better. Continuing to expand development has ushered in the problem of well spacing - how many wells, and how closely must they be spaced, to effectively deplete a shale reservoir? “Cube development” only increases the stakes; betting more dollars on upfront well spacing assumptions. While an operator will avoid the complicating factor of depletion, with all the Capex chips on red, so to speak. As some gamblers may know, in the long run, the house always wins. The same has proven true at the beginning of the second decade of shale development, the gamblers aren’t winning. Why not? To me, it comes down to fundamentals - the same issues that I saw as a data scientist - we are missing a key ingredient: Geomechanical Stress.
Understanding Stress
In order to understand well spacing, we need to understand the state of stress surrounding a well and the interactions created while stimulating and draining a volume of reservoir. In Dr. Zoback’s research, he does a fantastic job of blending theory, simulation, and empirical evidence to understand phenomena, leveraging all three. Dr. Zoback is able to identify the pattern, characterize it with key drivers, and connect those key drivers to the observations. He outlines and delivers an entire course on these key drivers, has published a textbook on the subject (Unconventional Reservoir Geomechanics), and collaborates with Petro.ai to create new geomechanics software tools (Dr. Zoback is our technical advisor on Geomechanics).
A very common problem is the lack of good data capture and interpretation in shale. I see lots of companies collect and store huge volumes of data, but these companies don’t take the time to interpret it. We may have an abundance of data, but most of it is bad: poorly organized and inaccessible. Further compounding the problem are engineers who are unable to quality control and make interpretations on collected data. As a result, engineers select from small volumes of good data, leading to an abundance of sampling bias in an industry that is overrun with data. My personal goal is to help customers use all of their collected data that holds great information but needs to be emancipated (I call this “dark data”).
Applying Geomechanics Understanding
I’ve had the great pleasure to work with Dr. Zoback for over a year, learning with him as we’ve tackled new and exciting use cases for our clients. I’m on the data and AI side, taking his concepts and scaling them to the level of operations a shale client requires, including handling complex development histories. The impact his research will have on this industry will be profound - it will be a central tenet for shale development.
Like most things in the physical world, hydraulic fractures want to open in the easiest direction. Stress is measured in pressure and there are three principal stresses that need to be accounted for in the reservoir:
- the minimum stress (Shmin)
- the maximum stress (SHmax) and
- the vertical stress (Sv).
The magnitude relationship between these stresses dictates the stress regime: normal, strike-slip, or reverse faulting. We can discern the vertical stress from the weight of the rock column, it’s hard to know SHmax, and we can measure Shmin (in most cases). In each of these regimes, the plane of the fault will be different because the fractures are opening in the direction with the least stresses.
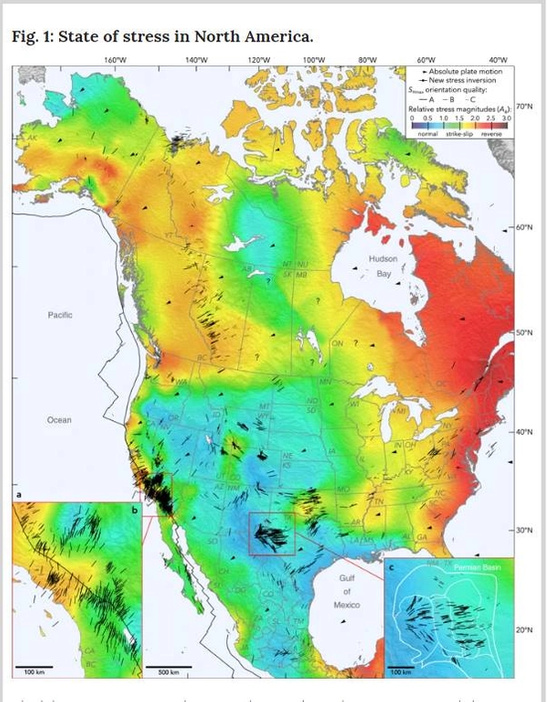
Orientation of SHmax and relative stress magnitudes across North America
Dr. Zoback and Dr. Lund Snee recently released a new publication that maps the orientation of SHmax and relative stress magnitudes across North America. Because SHmax is hard to interpret, they’ve done the hard work for us. Now, with their data set, if you measure Shmin (which we will explain later), you’ll be able to determine all three principal stresses in your asset.
We put this stress map in Petro.ai so you can easily reference this information across your asset. Understanding these principal stresses can have a dramatic affect when optimized: controlling for all other factors, wells drilled in the “correct direction” - 90 degrees from SHmax - perform 10-30% better.
When the pressure in the wellbore is higher than the minimum stress, it is easier for the fluid to fracture the rock and enter the reservoir as a frac than to stay in the wellbore. The wellbore pressure (measured as treating pressure at the surface) needs to overcome pressure loss over the perforations, cement issues along the wellbore, and stress shadow effects from neighboring fractures. The stress shadow effects can artificially raise the least principal stress, forcing a screen out or stopping fracture propagation.
The same logic applies vertically - whether or not you have stacked pay. In order to determine if the frac will stay in zone, you need to know the relative magnitudes of the stresses above and below the well. If the stress is lower above the well, the frac will go up; if the stress is lower below the well, the frac will go down. Many operators seem to assume that there are frac barriers (higher least principal stress) above and below a pay zone - this is very rare.
More likely, and in the most catastrophic scenario, you have an elevated pore pressure in your reservoir, increasing the productivity of the wells, but also causing hydraulic fractures to go both up and down (higher pore pressure increases Shmin). And, if you used the “bigger is better” strategy I described earlier, there are likely to be depletion affects across the whole pay zone. As infill wells are placed above and below, they will compete for shared resources with the original frac and you’ve overcapitalized your pad.
Using ISIPs to Improve Well Spacing
There are many factors that could lead to changes in the profile of minimum stress. Pore pressure, stress relaxation and depletion are your most common factors. In order to understand what is driving changes in least principal stress, you need to measure it over space and time. The most abundant (albeit noisy) data source is in 1-second frac van data.
At the end of a stage treatment, the treating pressure drops as the pumps turn off and the fractures close. There is a point called the Initial Shut-in Pressure “ISIP” that is commonly picked as part of the post-stage diagnostics by the pressure pumper. Due to operational considerations, high treating pressures, and lack of consistent theory (people still argue whether you should pick ISIP or fracture closure), ISIPs are rarely picked correctly and become a cloud of meaningless data.
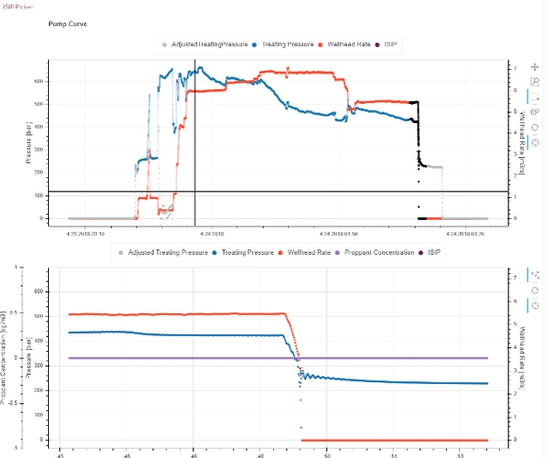
ISIP Picking Method in Petro.ai
At Petro.ai, we took time to develop a robust methodology for picking ISIPs after looking through thousands of stages by applying reasonable physical limitations of the pressure system. First, we account for friction loss across perforations, and second, we co-visualize the ISIP in reservoir conditions. Perforations present substantial friction - on the order of several thousand PSI - driven mostly by its radius.
As pumps shut off, the effect of this friction is removed over a very short time period. By adjusting treating pressures to “reservoir contact” we can gain a better picture of true net pressures (typically no more than 1,000 psi) and more realistic ISIPs. By visualizing the ISIP pick (with an uncertainty range) in the reservoir, we can instantly QC data to ensure it falls within a reasonable pressure gradient window (i.e. below the vertical stress and above hydrostatic).
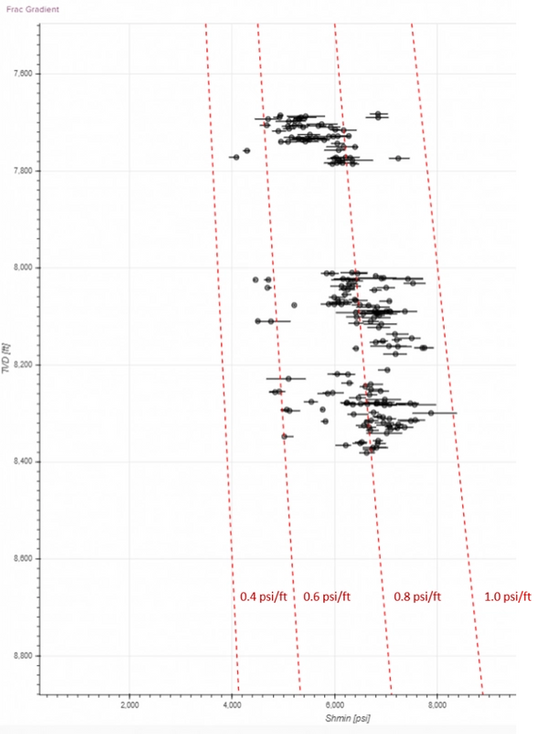
Vertical Stress Profile in Petro.ai
Whenever I hear a task should be automated, I hear an opportunity for it to be collaborated. You need to have a deeper discussion about your asset including ISIPs, frac gradients and your vertical stress profile. This is why Petro.ai has social comments and tags built into the interpretation process. Any “#tagged” data can easily be searched for and filtered upon.
As part of the social iteration engine, engineers and scientists can create different model scenarios to compare and contrast their ISIP interpretations and collaborate to develop more comprehensive interpretations. As Dr. Zoback says “just because you have a solution, it doesn’t mean you have understanding”.
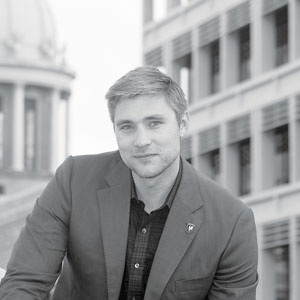
Troy Ruths, Ph.D, Founder & CEO, Petro.ai
Specialties: High performance computing, Machine learning, Software development, Optimization, Petroleum engineering, Data visualization, Scientific modelling, Data Management
Troy Ruths received his BS in Computer Science from Washington University in St. Louis and a PhD in Computer Science with a specialization in Computational Biology, from Rice University. He has over a decade of experience in data analysis of oil and gas applications and has managed the development and deployment of upstream-focused data analysis and visualization tools in 6 countries, representing shale gas, conventional oil, heavy oil, onshore, and deep offshore. He founded Petro.ai in 2013 as a conversion from his independent consulting practice.